Choosing the Right Surface Treatment for Stamping Tools
P-Tride™ | P-Wear ™ | MoST™ | Alcrona™ | TiN | TiCN | TiAIN
Balinit C | Electroless Nickel | CrN | nACVic
Wear resistant surface treatments offer great benefit to stamping tools when applied appropriately. While there are many good surface treatments and processes to choose from, Physical Vapor Deposition (PVD) coatings are ideally suited and typically the best option to use on precision slip and press fit punch components.
Selecting the right surface treatment and substrate tool steel combination is critical for achieving optimum tool life. PVD coatings provide excellent abrasion and galling resistance while maintaining the integrity of many substrate tool steels. These coatings work best when applied to high speed tool steels such as M-2, PM-M4, and T-15. A few select cold work tool steel grades can also be PVD coated successfully as long as they maintain at least a 60 HRC when tempered at or above 1,000 degrees Fahrenheit.
It is important to note that the PVD process is a line of sight process, which may limit the ability to coat interior contours and features. For these applications, nitriding, which case-hardens all exposed surfaces, is recommended.
Below is a list of standard surface treatments for stamping tools offered by Precision Punch & Tooling.
Additional coatings are available upon request.
Precision Punch & Tooling Enhancement Coatings
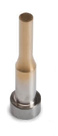
TiN – (Titanium Nitride) PVD Coating
Titanium nitride was the first general-purpose coating, and the PVD (physical vapor deposition) coating remains an extremely popular and inexpensive choice for wear resistant coatings on cutting tools, punching or forming applications. The TiN treatment provides excellent lubricity and wear resistance on cutting edges and wear surfaces.
Works best when used with lubricants.
Extreme micro hardness 2300 Vickers*.
TiN is not recommended for stainless steel, nickel or copper applications

TiCN – (Titanium CarboNitride) PVD Coating
Adding carbon to a TiN film creates a PVD coating that increases hardness by nearly 80%, resulting in extremely high wear resistance on cutting edges and wear surfaces. TiCN has the broadest range of applications among PVD coatings for enhanced performance and longer tool life.
Improved lubricity.
Extremely high micro hardness of 3000 Vickers*.
TiCN is recommended for stainless steel, nickel or copper applications.
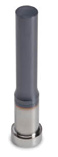
TiAlN – (Titanium Aluminum Nitride) PVD Coating
This is the coating of choice for high temperature applications where surface heat is generated. The aluminum in the film converts to aluminum oxide as the coating heats up, resulting in greater protection against shear stress and increased wear resistance on cutting edges. TiAIN coating is often used to protect dies and molds that are operated at high temperatures as in medium and hot forging and extrusion industries. High thermal stability.
Extremely high micro hardness of 3400 Vickers*.
Effectively used to machine titanium, aluminum and nickel alloys, stainless steels, alloy steels,
Co-Cr-Mo and cast
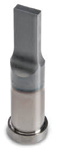
P-Tride™ – Nitride
This case-hardening surface treatment coats and toughens all outer tool surfaces. Its popularity is derived from a large range of effective case applications available at a relatively small cost. Because P-Tride™ case-hardens all exposed surfaces without relying on line of sight (such as with the PVD process), it is extremely effective for coating items such as buttons and tools.
Ideal for increasing surface hardness by approximately 10 points HRC.
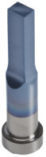
P-Wear Optimum™
A proprietary Quad coating with pre and post processing designed to enhance tool performance.
- Nano hardness 3600 HV
- Thickness 2-3 microns
- .25 coefficient of friction
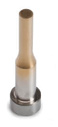
P-Wear™
This is a dual-process surface treatment/coating process. By providing an extremely hard coating on top of a less hard but tough surface treatment, load is distributed throughout the tool. This can prevent premature tool failure in applications, such as extracting or forming, where tools endure isolated stress or load on small areas.
Provides excellent toughness with high micro hardness of 2300 Vickers*.
P-Wear™ is not recommended for use in stainless steel, nickel and copper applications and is most effective when used with lubricants.
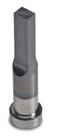
MoST™ – (Titanium CarboNitride with Molybdenum Disulfide)
PVD w/Moly Top Coating
MoST™ coating provides longer tool life through reduced operating friction and galling. The highly lubricious top layer coat is perfect for stamping of pre-painted material and plated material applications.
Offers extremely high lubricity.
Provides micro hardness of 2000 Vickers*.
MoST™ is especially effective with stainless, HSLA grades, and high tensile strength stainless.
MoST™ also offers an additional special heat treatment enhancement process to optimize toughness.
MoST™ is a trademark of IonBond® Inc.
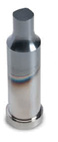
Alcrona™ – (Aluminum Chromium Nitride) PVD Coating
This multifunctional aluminum and chromium coating is ideal for a very wide variety of high temperature and high strength cutting tools and for punching and forming applications. The treatment creates excellent wear resistance, thermal shock stability and high hot hardness properties. The enhanced performance is due to the advantages of thermal stability, low coefficient of friction, and ductility.
Exceptionally low coefficient of friction.
Extraordinary high thermal ability.
Extremely high micro hardness of 3400 Vickers*.
Alcrona™ is a trademark of Oerlikon Balzers.
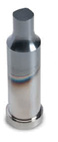
CrN - Chrome Nitride Coating
This coating has excellent adhesion, high toughness, and good corrosion resistance. Typical applications are metal forming, metal die casting, and plastic injection molding. Approximate hardness is 1800-2100 Vickers*.
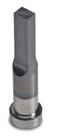
nACVic Coating
This coating is used for forming and punching applications for high alloyed materials. The coating offers a low coefficient of friction and therefore offers improved wear resistance. Approximate hardness is 4000 Vickers*.
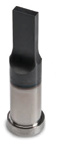
Balinit C Coating
This coating is a WC/C-based coating, and thus a mixture of metal and diamond-like carbon. Results in reduced surface fatigue tribo-oxidation, thereby reducing adhesive wear and good sliding properties due to a low coefficient of friction.
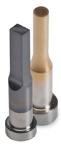
Electroless Nickel Coating
Depending on customer application combined with low, medium or high levels of Phosphorous, provides corrosion resistance and offers wear protection. Electroless Nickel PTFE (Teflon) plated in a medium level Phosphorous bath provides lubricity and mold release properties for low-temp injection mold operations. Electroless Nickel Boron provides maximum hardness and self-lubrication for anti-galling properties.